UMS Gas Radial Engine Enthusiasts Rabbit Hole
#76

Hello AllHappy to see the thread is getting some good use. I have finally fired my 125 for initial break in. Have run the first gallon at 32:1 in short heat cycles under 4000 rpm as the manual recommended. No issues thus far. Initial start was a little tedious. Took 17 flips to get a burp. 5 then seven to start off idle. Not too bad.
Made runs with engine mounted on the Phoenix Waco secured with wings assembled. If anything done differently, I would have run it in in on a stand. That much static pressure on this ARF airframe was un necessary.
I intend to fortify the wing perches and add some supports to it before flight. I ran it in cowl off. I am creating a aluminum plate baffle to mount inside the cowl. Temps were ok without the cowl 150-170 degrees, but don't want to run it hot in the air. Haven't baffled my other radials, but never ran full cowls.
Over all pleased. The cadence and run up sounds are awesome. Pukes a little goo out of the lifter blocks. I have been pulling both pre runs and lubing the cam trails. Been lubing the pushrods every run cycle to let them wear in easy. Valves still don't need adjustment. Packing nuts have been stationary. #3 required a touch and leaks lightly, but resisting monkey tightening lol.
Caught one adjuster lock nut a little loose but not a complaint. See how it acts when tuned to 40:1 Amsoil.
Report back in after that.
Aaron-
Made runs with engine mounted on the Phoenix Waco secured with wings assembled. If anything done differently, I would have run it in in on a stand. That much static pressure on this ARF airframe was un necessary.
I intend to fortify the wing perches and add some supports to it before flight. I ran it in cowl off. I am creating a aluminum plate baffle to mount inside the cowl. Temps were ok without the cowl 150-170 degrees, but don't want to run it hot in the air. Haven't baffled my other radials, but never ran full cowls.
Over all pleased. The cadence and run up sounds are awesome. Pukes a little goo out of the lifter blocks. I have been pulling both pre runs and lubing the cam trails. Been lubing the pushrods every run cycle to let them wear in easy. Valves still don't need adjustment. Packing nuts have been stationary. #3 required a touch and leaks lightly, but resisting monkey tightening lol.
Caught one adjuster lock nut a little loose but not a complaint. See how it acts when tuned to 40:1 Amsoil.
Report back in after that.
Aaron-
#77

My Feedback: (3)

I see you are putting your engine in the Phoenix Waco 60cc, I am putting my UMS 7-90 into the same plane. The firewall in this plane doesn't seem to be as solid as I would like it, do you think you will be re-enforcing that too? I might throw some extra angle wood on mine.
As for cooling, I was seeing cylinder temps too anywhere from 140F to 220F on my test stand in open air depending on how hard I was running it. I am a little worried about what temp it may reach inside the cowl. I might baffle mine too, I haven't decided yet. I know it will be ugly but I was thinking of shaving off 1/4" of fiberglass off the back of the cowl to let even more air escape. I'd rather not overheat in the air, and if I have to sacrifice a little bit of looks to make that happen then thats fine with me.
The valve area on the heads of mine gets wet and drips black goo. I guess thats normal as thats lubrication coming up to lube the valve guides.
As for cooling, I was seeing cylinder temps too anywhere from 140F to 220F on my test stand in open air depending on how hard I was running it. I am a little worried about what temp it may reach inside the cowl. I might baffle mine too, I haven't decided yet. I know it will be ugly but I was thinking of shaving off 1/4" of fiberglass off the back of the cowl to let even more air escape. I'd rather not overheat in the air, and if I have to sacrifice a little bit of looks to make that happen then thats fine with me.
The valve area on the heads of mine gets wet and drips black goo. I guess thats normal as thats lubrication coming up to lube the valve guides.
Hello AllHappy to see the thread is getting some good use. I have finally fired my 125 for initial break in. Have run the first gallon at 32:1 in short heat cycles under 4000 rpm as the manual recommended. No issues thus far. Initial start was a little tedious. Took 17 flips to get a burp. 5 then seven to start off idle. Not too bad.
Made runs with engine mounted on the Phoenix Waco secured with wings assembled. If anything done differently, I would have run it in in on a stand. That much static pressure on this ARF airframe was un necessary.
I intend to fortify the wing perches and add some supports to it before flight. I ran it in cowl off. I am creating a aluminum plate baffle to mount inside the cowl. Temps were ok without the cowl 150-170 degrees, but don't want to run it hot in the air. Haven't baffled my other radials, but never ran full cowls.
Over all pleased. The cadence and run up sounds are awesome. Pukes a little goo out of the lifter blocks. I have been pulling both pre runs and lubing the cam trails. Been lubing the pushrods every run cycle to let them wear in easy. Valves still don't need adjustment. Packing nuts have been stationary. #3 required a touch and leaks lightly, but resisting monkey tightening lol.
Caught one adjuster lock nut a little loose but not a complaint. See how it acts when tuned to 40:1 Amsoil.
Report back in after that.
Aaron-
https://youtu.be/7QePUWS1fn0
Made runs with engine mounted on the Phoenix Waco secured with wings assembled. If anything done differently, I would have run it in in on a stand. That much static pressure on this ARF airframe was un necessary.
I intend to fortify the wing perches and add some supports to it before flight. I ran it in cowl off. I am creating a aluminum plate baffle to mount inside the cowl. Temps were ok without the cowl 150-170 degrees, but don't want to run it hot in the air. Haven't baffled my other radials, but never ran full cowls.
Over all pleased. The cadence and run up sounds are awesome. Pukes a little goo out of the lifter blocks. I have been pulling both pre runs and lubing the cam trails. Been lubing the pushrods every run cycle to let them wear in easy. Valves still don't need adjustment. Packing nuts have been stationary. #3 required a touch and leaks lightly, but resisting monkey tightening lol.
Caught one adjuster lock nut a little loose but not a complaint. See how it acts when tuned to 40:1 Amsoil.
Report back in after that.
Aaron-
https://youtu.be/7QePUWS1fn0
#78

Hello Timbers
Thoughts on the ARF . I trust you have read the threads about failures of this Phoenix offering as with the Lysander ARF also. Seems complaints have pointed to wing loading failures. The firewall build looks acceptable to me on this one. I obtained it used from a person who had flown it a number of times successfully. I sought one out used for that porpoise to hopefully get one "proven" before mounting this high investment motor. My brother in law has one that has flown successfully with a large DLE twin on it . He did not want to part with it. So I ended up with this one and traveled to get it. It was flown with an electric motor. The stresses with this gas radial will be obviously greater and loading higher. My concerns lie more in the lower wing perches and support tubes. Another owner has stripped the wing bottoms to inspect and fortify glue joints on the ribs. I think that is what I should do also, but the interior fortification of the perches and tube tables are non destructive and I am sad with recovering wings so I may stop there.
I have run this monster 1.5 hours chained down and the firewall looks solid under the static load. I assume it will be ok in the air in that area.
With the power of our chosen engines, I don't have a lot of concern about adding some weight. Certainly couldnt hurt to to strengthen the front end eh? I'd go for it if I were you.
Your motor will be even smoother with more cylinders and mass. But it couldn't hurt to strengthen.
I am just doing the baffle for safety sake with a new engine and to be compliant with the UMS documentation. i cut this out and intend to mount to the cowl interior. I don't intend to open the cowl on the outgoing side. There is a lot of exit opening around the two exhaust ring discharge points well directing the flow to also cool the ring (hopefully).
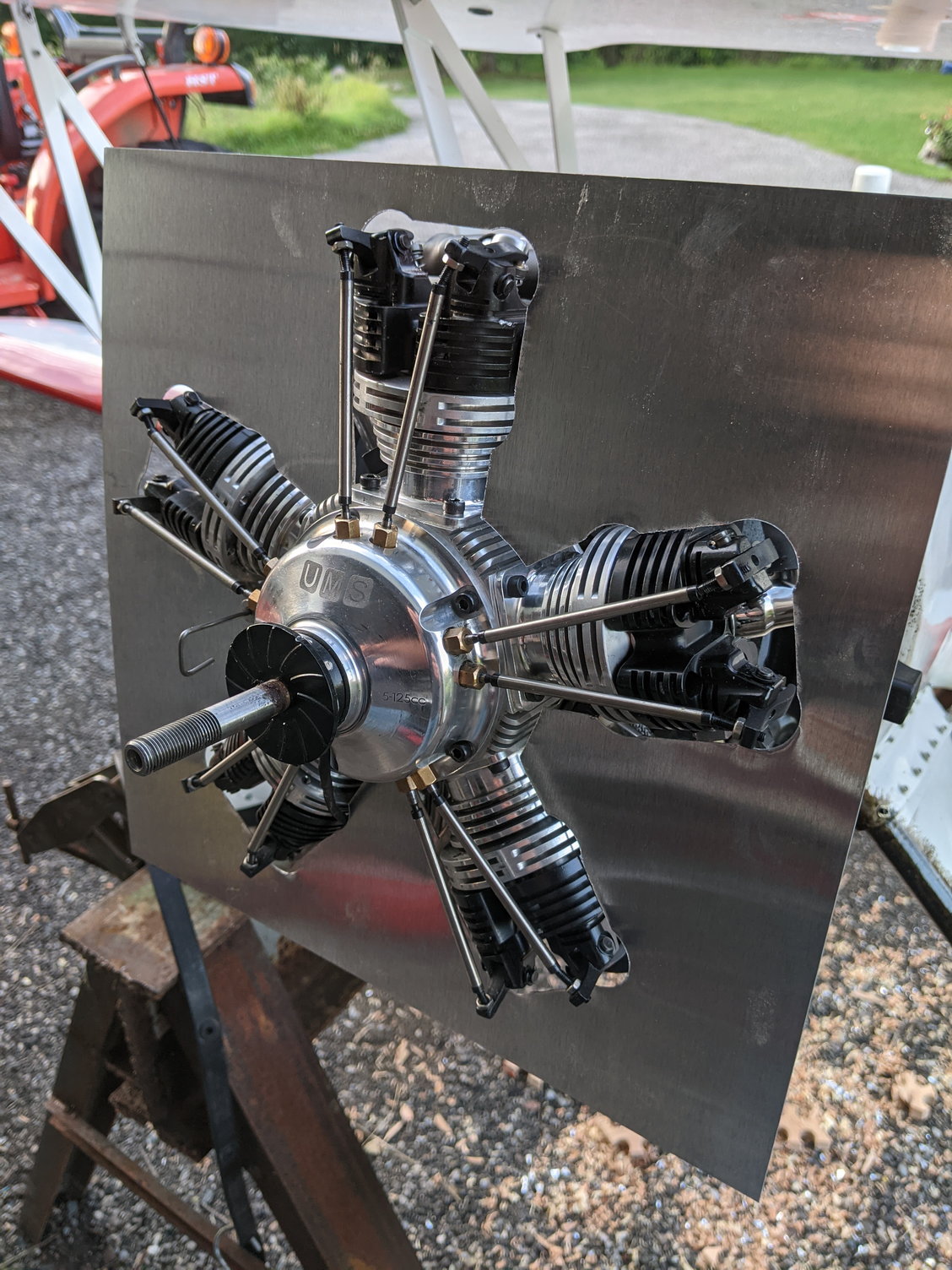
I don't care for the look of the baffle but it should be very functional at directing the cooling air across the heads fins and heat sinks on the crankcase.
May remove it down the road but for now I am planning on running it baffled.
Just my paranoia kicking in lol.
Thanks for your contribution to this thread. Your input as with others is valuable in all of our hopeful successes.
Aaron-
Thoughts on the ARF . I trust you have read the threads about failures of this Phoenix offering as with the Lysander ARF also. Seems complaints have pointed to wing loading failures. The firewall build looks acceptable to me on this one. I obtained it used from a person who had flown it a number of times successfully. I sought one out used for that porpoise to hopefully get one "proven" before mounting this high investment motor. My brother in law has one that has flown successfully with a large DLE twin on it . He did not want to part with it. So I ended up with this one and traveled to get it. It was flown with an electric motor. The stresses with this gas radial will be obviously greater and loading higher. My concerns lie more in the lower wing perches and support tubes. Another owner has stripped the wing bottoms to inspect and fortify glue joints on the ribs. I think that is what I should do also, but the interior fortification of the perches and tube tables are non destructive and I am sad with recovering wings so I may stop there.
I have run this monster 1.5 hours chained down and the firewall looks solid under the static load. I assume it will be ok in the air in that area.
With the power of our chosen engines, I don't have a lot of concern about adding some weight. Certainly couldnt hurt to to strengthen the front end eh? I'd go for it if I were you.
Your motor will be even smoother with more cylinders and mass. But it couldn't hurt to strengthen.
I am just doing the baffle for safety sake with a new engine and to be compliant with the UMS documentation. i cut this out and intend to mount to the cowl interior. I don't intend to open the cowl on the outgoing side. There is a lot of exit opening around the two exhaust ring discharge points well directing the flow to also cool the ring (hopefully).
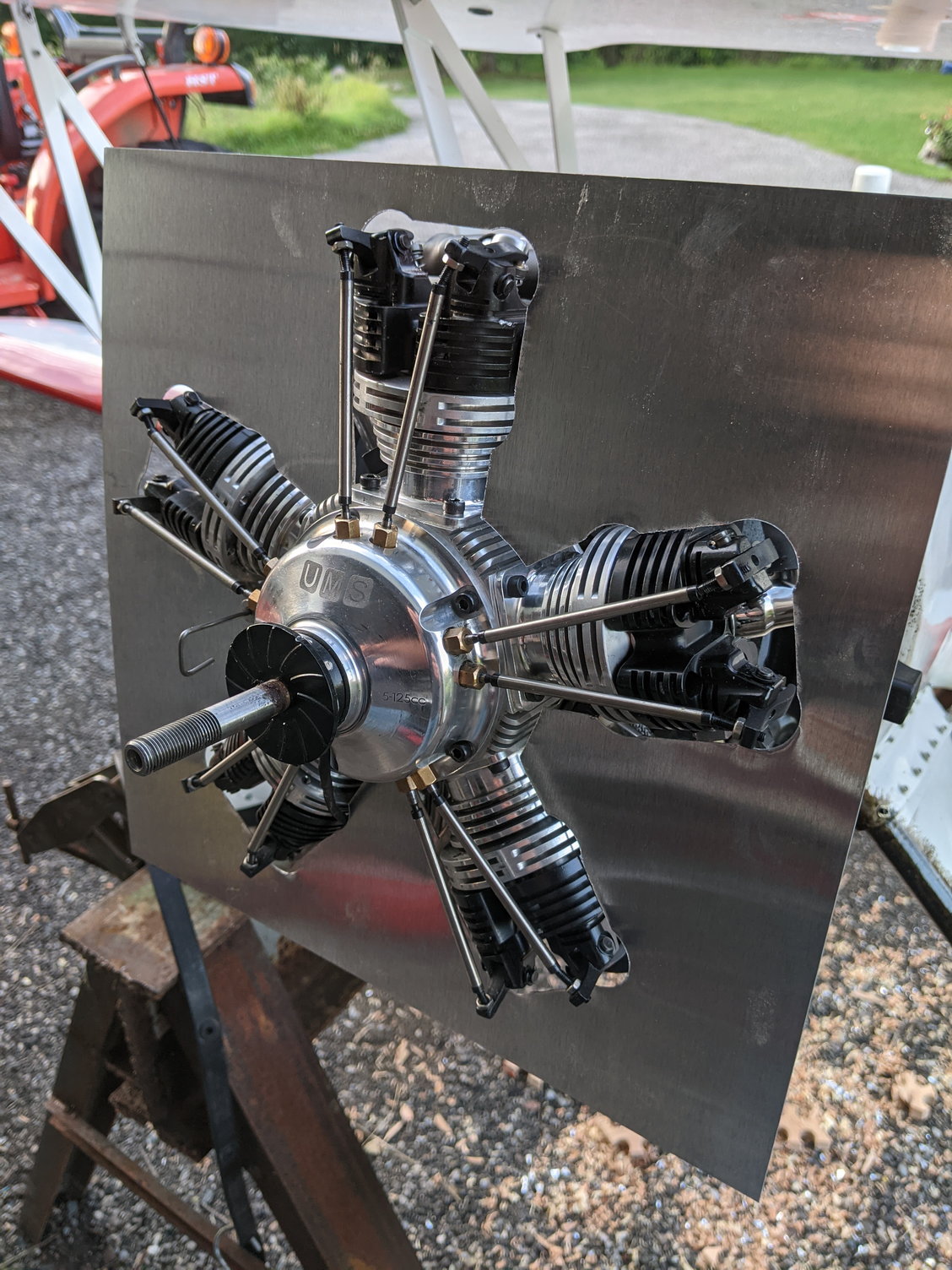
I don't care for the look of the baffle but it should be very functional at directing the cooling air across the heads fins and heat sinks on the crankcase.
May remove it down the road but for now I am planning on running it baffled.
Just my paranoia kicking in lol.
Thanks for your contribution to this thread. Your input as with others is valuable in all of our hopeful successes.
Aaron-
#79

Hello Timbers
Thoughts on the ARF . I trust you have read the threads about failures of this Phoenix offering as with the Lysander ARF also. Seems complaints have pointed to wing loading failures. The firewall build looks acceptable to me on this one. I obtained it used from a person who had flown it a number of times successfully. I sought one out used for that porpoise to hopefully get one "proven" before mounting this high investment motor. My brother in law has one that has flown successfully with a large DLE twin on it . He did not want to part with it. So I ended up with this one and traveled to get it. It was flown with an electric motor. The stresses with this gas radial will be obviously greater and loading higher. My concerns lie more in the lower wing perches and support tubes. Another owner has stripped the wing bottoms to inspect and fortify glue joints on the ribs. I think that is what I should do also, but the interior fortification of the perches and tube tables are non destructive and I am sad with recovering wings so I may stop there.
I have run this monster 1.5 hours chained down and the firewall looks solid under the static load. I assume it will be ok in the air in that area.
With the power of our chosen engines, I don't have a lot of concern about adding some weight. Certainly couldnt hurt to to strengthen the front end eh? I'd go for it if I were you.
Your motor will be even smoother with more cylinders and mass. But it couldn't hurt to strengthen.
I am just doing the baffle for safety sake with a new engine and to be compliant with the UMS documentation. i cut this out and intend to mount to the cowl interior. I don't intend to open the cowl on the outgoing side. There is a lot of exit opening around the two exhaust ring discharge points well directing the flow to also cool the ring (hopefully).
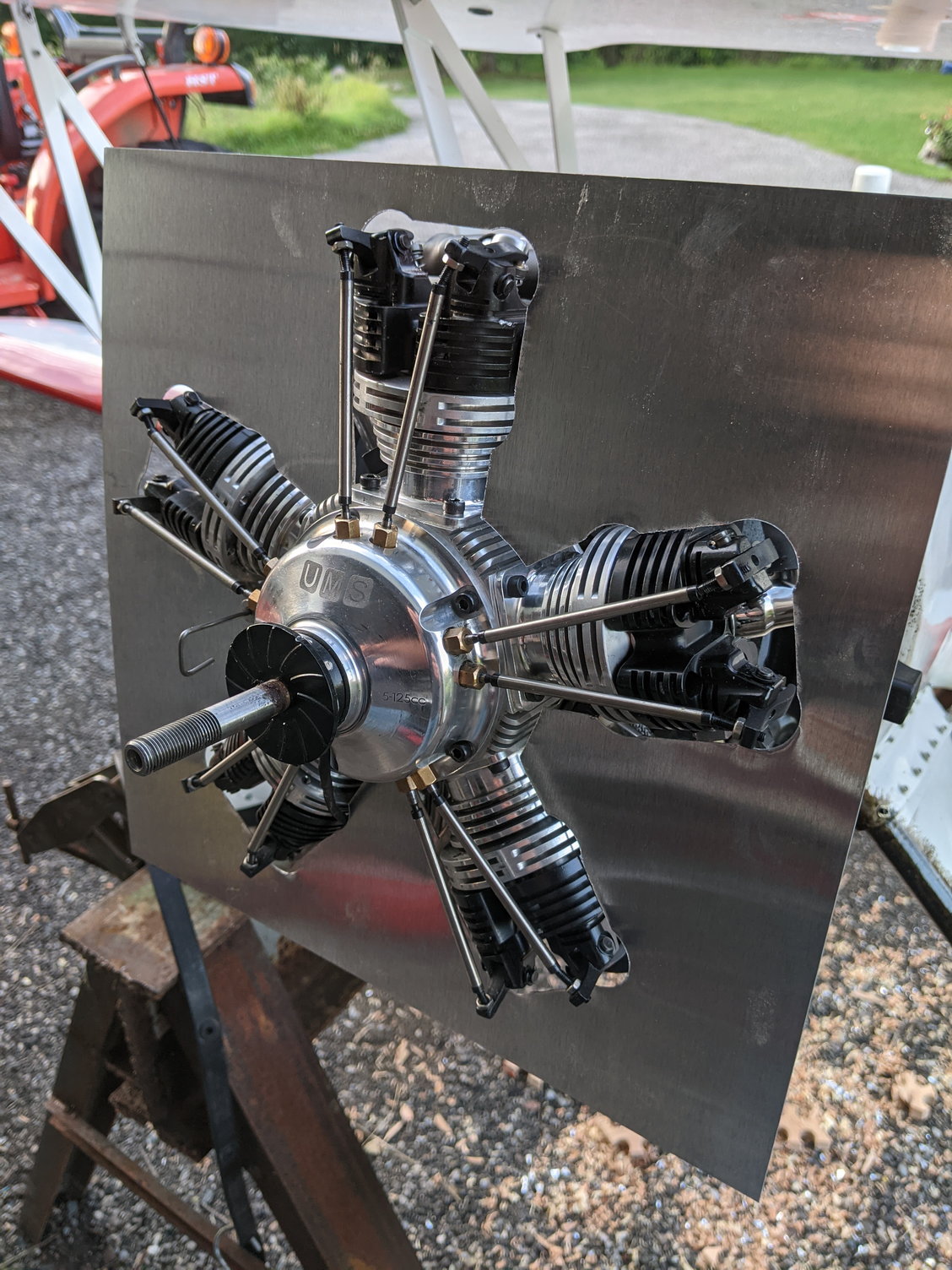
I don't care for the look of the baffle but it should be very functional at directing the cooling air across the heads fins and heat sinks on the crankcase.
May remove it down the road but for now I am planning on running it baffled.
Just my paranoia kicking in lol.
Thanks for your contribution to this thread. Your input as with others is valuable in all of our hopeful successes.
Aaron-
Thoughts on the ARF . I trust you have read the threads about failures of this Phoenix offering as with the Lysander ARF also. Seems complaints have pointed to wing loading failures. The firewall build looks acceptable to me on this one. I obtained it used from a person who had flown it a number of times successfully. I sought one out used for that porpoise to hopefully get one "proven" before mounting this high investment motor. My brother in law has one that has flown successfully with a large DLE twin on it . He did not want to part with it. So I ended up with this one and traveled to get it. It was flown with an electric motor. The stresses with this gas radial will be obviously greater and loading higher. My concerns lie more in the lower wing perches and support tubes. Another owner has stripped the wing bottoms to inspect and fortify glue joints on the ribs. I think that is what I should do also, but the interior fortification of the perches and tube tables are non destructive and I am sad with recovering wings so I may stop there.
I have run this monster 1.5 hours chained down and the firewall looks solid under the static load. I assume it will be ok in the air in that area.
With the power of our chosen engines, I don't have a lot of concern about adding some weight. Certainly couldnt hurt to to strengthen the front end eh? I'd go for it if I were you.
Your motor will be even smoother with more cylinders and mass. But it couldn't hurt to strengthen.
I am just doing the baffle for safety sake with a new engine and to be compliant with the UMS documentation. i cut this out and intend to mount to the cowl interior. I don't intend to open the cowl on the outgoing side. There is a lot of exit opening around the two exhaust ring discharge points well directing the flow to also cool the ring (hopefully).
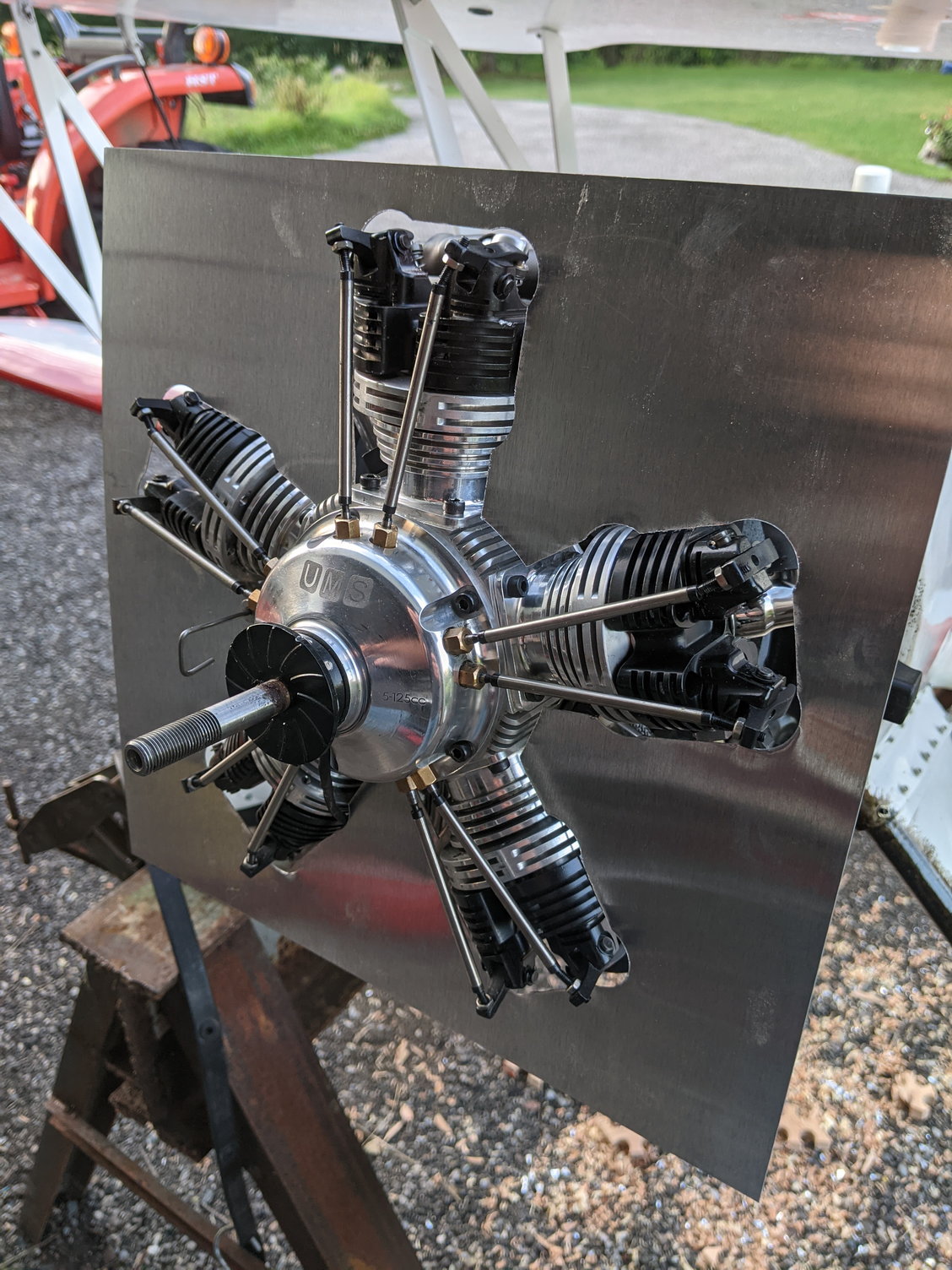
I don't care for the look of the baffle but it should be very functional at directing the cooling air across the heads fins and heat sinks on the crankcase.
May remove it down the road but for now I am planning on running it baffled.
Just my paranoia kicking in lol.
Thanks for your contribution to this thread. Your input as with others is valuable in all of our hopeful successes.
Aaron-
For a proper and effective baffle, you will have to "tunnel" the cylinders such that the air has to stay in contact with the fins.
It looks like an awful lot of work and extremely fragile, but it surprised me that I built the entire thing out of 2mm Balsa in about 2~2,5 hours using simple quick drying Aliphatic glue. Just cut and paste as you go along, really straightforward.
The thing looks absolutely filigrane and fragile, so it surprised me a 2nd time that once it was fixated in the cowling, the whole thing was pretty much rocksolid while weighing next to nothing (it added some 50 grammes to the cowling all in all).
And that is including a thin coat of Epoxy resin to oil-proof it, and a single coat of matt black paint.
Last edited by 1967brutus; 08-10-2022 at 12:37 AM.
#80

With all due respect, that is NOT an effective baffle.... It is better than nothing, but all it will do is force the cooling air to "touch" the fins at the location of the baffle. As soon as the air has passed through that restriction, it is going to spread out in the wide open space behind the baffle and lose its velocity AND its incentive to follow the fins.
For a proper and effective baffle, you will have to "tunnel" the cylinders such that the air has to stay in contact with the fins.
Attachment 2272128
Attachment 2272129
Attachment 2272130
Attachment 2272131
Attachment 2272132
It looks like an awful lot of work and extremely fragile, but it surprised me that I built the entire thing out of 2mm Balsa in about 2~2,5 hours using simple quick drying Aliphatic glue. Just cut and paste as you go along, really straightforward.
The thing looks absolutely filigrane and fragile, so it surprised me a 2nd time that once it was fixated in the cowling, the whole thing was pretty much rocksolid while weighing next to nothing (it added some 50 grammes to the cowling all in all).
And that is including a thin coat of Epoxy resin to oil-proof it, and a single coat of matt black paint.
For a proper and effective baffle, you will have to "tunnel" the cylinders such that the air has to stay in contact with the fins.
Attachment 2272128
Attachment 2272129
Attachment 2272130
Attachment 2272131
Attachment 2272132
It looks like an awful lot of work and extremely fragile, but it surprised me that I built the entire thing out of 2mm Balsa in about 2~2,5 hours using simple quick drying Aliphatic glue. Just cut and paste as you go along, really straightforward.
The thing looks absolutely filigrane and fragile, so it surprised me a 2nd time that once it was fixated in the cowling, the whole thing was pretty much rocksolid while weighing next to nothing (it added some 50 grammes to the cowling all in all).
And that is including a thin coat of Epoxy resin to oil-proof it, and a single coat of matt black paint.
#81

Thanks... I got the inspiration from seeing how real radials were being cooled. Some of those are "wrapped" in very tight fitting cooling ducts with very minimal air inlet openings.
I did some calculations on it, based on estimated velocities that seem to indicate that the pressure build-up in the intake of the cowling is around 3,5~4 Milibar (something like 0,055 psi), and an air massflow of .4 kilo/sec (1 lbs/sec)
I have no way of measuring that pressure or airflow, but the calculated resulting temperature rise of about 10 deg C (18F) turned out to be near spot on.
But I have to correct my own words: I looked in my notes and I see the total building time was two times 2,5 hrs. In my memory I did it in one session, turns out it was two of those...
I did some calculations on it, based on estimated velocities that seem to indicate that the pressure build-up in the intake of the cowling is around 3,5~4 Milibar (something like 0,055 psi), and an air massflow of .4 kilo/sec (1 lbs/sec)
I have no way of measuring that pressure or airflow, but the calculated resulting temperature rise of about 10 deg C (18F) turned out to be near spot on.
But I have to correct my own words: I looked in my notes and I see the total building time was two times 2,5 hrs. In my memory I did it in one session, turns out it was two of those...
#82
Junior Member

Thanks... I got the inspiration from seeing how real radials were being cooled. Some of those are "wrapped" in very tight fitting cooling ducts with very minimal air inlet openings.
I did some calculations on it, based on estimated velocities that seem to indicate that the pressure build-up in the intake of the cowling is around 3,5~4 Milibar (something like 0,055 psi), and an air massflow of .4 kilo/sec (1 lbs/sec)
I have no way of measuring that pressure or airflow, but the calculated resulting temperature rise of about 10 deg C (18F) turned out to be near spot on.
But I have to correct my own words: I looked in my notes and I see the total building time was two times 2,5 hrs. In my memory I did it in one session, turns out it was two of those...
I did some calculations on it, based on estimated velocities that seem to indicate that the pressure build-up in the intake of the cowling is around 3,5~4 Milibar (something like 0,055 psi), and an air massflow of .4 kilo/sec (1 lbs/sec)
I have no way of measuring that pressure or airflow, but the calculated resulting temperature rise of about 10 deg C (18F) turned out to be near spot on.
But I have to correct my own words: I looked in my notes and I see the total building time was two times 2,5 hrs. In my memory I did it in one session, turns out it was two of those...

The following users liked this post:
Propflux01 (08-10-2022)
#84

Thanks... I got the inspiration from seeing how real radials were being cooled. Some of those are "wrapped" in very tight fitting cooling ducts with very minimal air inlet openings.
I did some calculations on it, based on estimated velocities that seem to indicate that the pressure build-up in the intake of the cowling is around 3,5~4 Milibar (something like 0,055 psi), and an air massflow of .4 kilo/sec (1 lbs/sec)
I have no way of measuring that pressure or airflow, but the calculated resulting temperature rise of about 10 deg C (18F) turned out to be near spot on.
But I have to correct my own words: I looked in my notes and I see the total building time was two times 2,5 hrs. In my memory I did it in one session, turns out it was two of those...
I did some calculations on it, based on estimated velocities that seem to indicate that the pressure build-up in the intake of the cowling is around 3,5~4 Milibar (something like 0,055 psi), and an air massflow of .4 kilo/sec (1 lbs/sec)
I have no way of measuring that pressure or airflow, but the calculated resulting temperature rise of about 10 deg C (18F) turned out to be near spot on.
But I have to correct my own words: I looked in my notes and I see the total building time was two times 2,5 hrs. In my memory I did it in one session, turns out it was two of those...
It is pretty easy to add sidewalls to my flat aluminum plate., Would like to know if it is actually necessary. Poking around, flat plates and tabs seem common on other rc engine set ups. More have none at all. Spinner design and size does not seem to consistent between setups and haven't even seen a mention of the effect in any of my user manuals. Also very few spinners used by other modellers. Are we going to extremes here?
Respectfully
Aaron-
#85

Curious. Did you do temp testing on the set up before and after the addition of the tunnelling to obtain actual effective temperature reduction at the heads and front bell bearings/ cams?
It is pretty easy to add sidewalls to my flat aluminum plate., Would like to know if it is actually necessary. Poking around, flat plates and tabs seem common on other rc engine set ups. More have none at all. Spinner design and size does not seem to consistent between setups and haven't even seen a mention of the effect in any of my user manuals. Also very few spinners used by other modellers. Are we going to extremes here?
Respectfully
Aaron-
It is pretty easy to add sidewalls to my flat aluminum plate., Would like to know if it is actually necessary. Poking around, flat plates and tabs seem common on other rc engine set ups. More have none at all. Spinner design and size does not seem to consistent between setups and haven't even seen a mention of the effect in any of my user manuals. Also very few spinners used by other modellers. Are we going to extremes here?
Respectfully
Aaron-
I only tested with fully exposed engine, versus "cowled and fully baffled/tunneled" and the differences were rather significant.
Peak RPM on the ground is 5600 RPM. Minimum RPM for sustained level flight is 4000 RPM.
With exposed engine, I could run a ground RPM of a touch over 4K continuous, in the air that continuous sustainable RPM rose to 5200 RPM (so safe enough to fly but no reserve) and coming from a temperature stabilized 4000 RPM, I could run WOT (6500 in the air) for about 30 seconds, maybe 40.
With fully cowled and baffled/tunneled engine, on the ground the engine would hold 4500 RPM continuous (500 RPM increase over exposed), continuous sustainable in the air was at approx 5900 RPM (700 RPM gain) Peak RPM increased to 6800~6900 RPM, and coming from temperature stabilized 4000, I could run WOT for at least a minute or more. Did not even follow that through till the end, to be honest. 1 minute is long enough when you're a bit stressed...

Since peak RPM increased due to reduced drag/greater airspeed, that means power and heat production went up, but despite that the allowable time for WOT more than doubled.
The front bell/cam area should be a non-issue WRT cooling. That area of the engine should not need ANY additional cooling. If it does, that would indicate a mechanical problem there (bad bearing etc) or a lubrication issue.
I have been poking around on the various fields as well, and I noticed that many people baffle, or don't baffle, and claim their cooling works but I never see telemetry or temperature probes. So I take that all a bit with a grain of salt.
Cowl shapes vary greatly, and where a Waco or Lysander has a cowl that most likely won't affect cooling at all, an FW190 has a cowlshape that makes it near literally impossible to run a radial without bafling/tunneling. The real thing couldn't do it either (the original actually had a very cleverly designed cooling "system").
#86


Aaron, That lovely, flat aluminum baffle is a great start. You are quite correct in that some wraparound tunneling would perform very well. Also should prove to be light and durable. I would be very happy to drive over and lend a hand .
#87

I did do temperature testing, but cannot give a "before/after" temperature, because my engine was never intended to be operated on gasoline, so it runs HOT. What I do know "before/after" is what RPM I could run on the ground up to the temperature limit I set myself (based on experience with other converted ASP engines of similar build quality and material selection), the RPMs I could run continuously in the air before/after, and how long it would take at full throttle until the limit was reached.
I only tested with fully exposed engine, versus "cowled and fully baffled/tunneled" and the differences were rather significant.
Peak RPM on the ground is 5600 RPM. Minimum RPM for sustained level flight is 4000 RPM.
With exposed engine, I could run a ground RPM of a touch over 4K continuous, in the air that continuous sustainable RPM rose to 5200 RPM (so safe enough to fly but no reserve) and coming from a temperature stabilized 4000 RPM, I could run WOT (6500 in the air) for about 30 seconds, maybe 40.
With fully cowled and baffled/tunneled engine, on the ground the engine would hold 4500 RPM continuous (500 RPM increase over exposed), continuous sustainable in the air was at approx 5900 RPM (700 RPM gain) Peak RPM increased to 6800~6900 RPM, and coming from temperature stabilized 4000, I could run WOT for at least a minute or more. Did not even follow that through till the end, to be honest. 1 minute is long enough when you're a bit stressed...
Since peak RPM increased due to reduced drag/greater airspeed, that means power and heat production went up, but despite that the allowable time for WOT more than doubled.
The front bell/cam area should be a non-issue WRT cooling. That area of the engine should not need ANY additional cooling. If it does, that would indicate a mechanical problem there (bad bearing etc) or a lubrication issue.
I have been poking around on the various fields as well, and I noticed that many people baffle, or don't baffle, and claim their cooling works but I never see telemetry or temperature probes. So I take that all a bit with a grain of salt.
Cowl shapes vary greatly, and where a Waco or Lysander has a cowl that most likely won't affect cooling at all, an FW190 has a cowlshape that makes it near literally impossible to run a radial without bafling/tunneling. The real thing couldn't do it either (the original actually had a very cleverly designed cooling "system").
I only tested with fully exposed engine, versus "cowled and fully baffled/tunneled" and the differences were rather significant.
Peak RPM on the ground is 5600 RPM. Minimum RPM for sustained level flight is 4000 RPM.
With exposed engine, I could run a ground RPM of a touch over 4K continuous, in the air that continuous sustainable RPM rose to 5200 RPM (so safe enough to fly but no reserve) and coming from a temperature stabilized 4000 RPM, I could run WOT (6500 in the air) for about 30 seconds, maybe 40.
With fully cowled and baffled/tunneled engine, on the ground the engine would hold 4500 RPM continuous (500 RPM increase over exposed), continuous sustainable in the air was at approx 5900 RPM (700 RPM gain) Peak RPM increased to 6800~6900 RPM, and coming from temperature stabilized 4000, I could run WOT for at least a minute or more. Did not even follow that through till the end, to be honest. 1 minute is long enough when you're a bit stressed...

Since peak RPM increased due to reduced drag/greater airspeed, that means power and heat production went up, but despite that the allowable time for WOT more than doubled.
The front bell/cam area should be a non-issue WRT cooling. That area of the engine should not need ANY additional cooling. If it does, that would indicate a mechanical problem there (bad bearing etc) or a lubrication issue.
I have been poking around on the various fields as well, and I noticed that many people baffle, or don't baffle, and claim their cooling works but I never see telemetry or temperature probes. So I take that all a bit with a grain of salt.
Cowl shapes vary greatly, and where a Waco or Lysander has a cowl that most likely won't affect cooling at all, an FW190 has a cowlshape that makes it near literally impossible to run a radial without bafling/tunneling. The real thing couldn't do it either (the original actually had a very cleverly designed cooling "system").
#88

peessHaving a great summer with Claude and the Fr300 on the GP PT 17. Hope your getting in plenty stick time too!
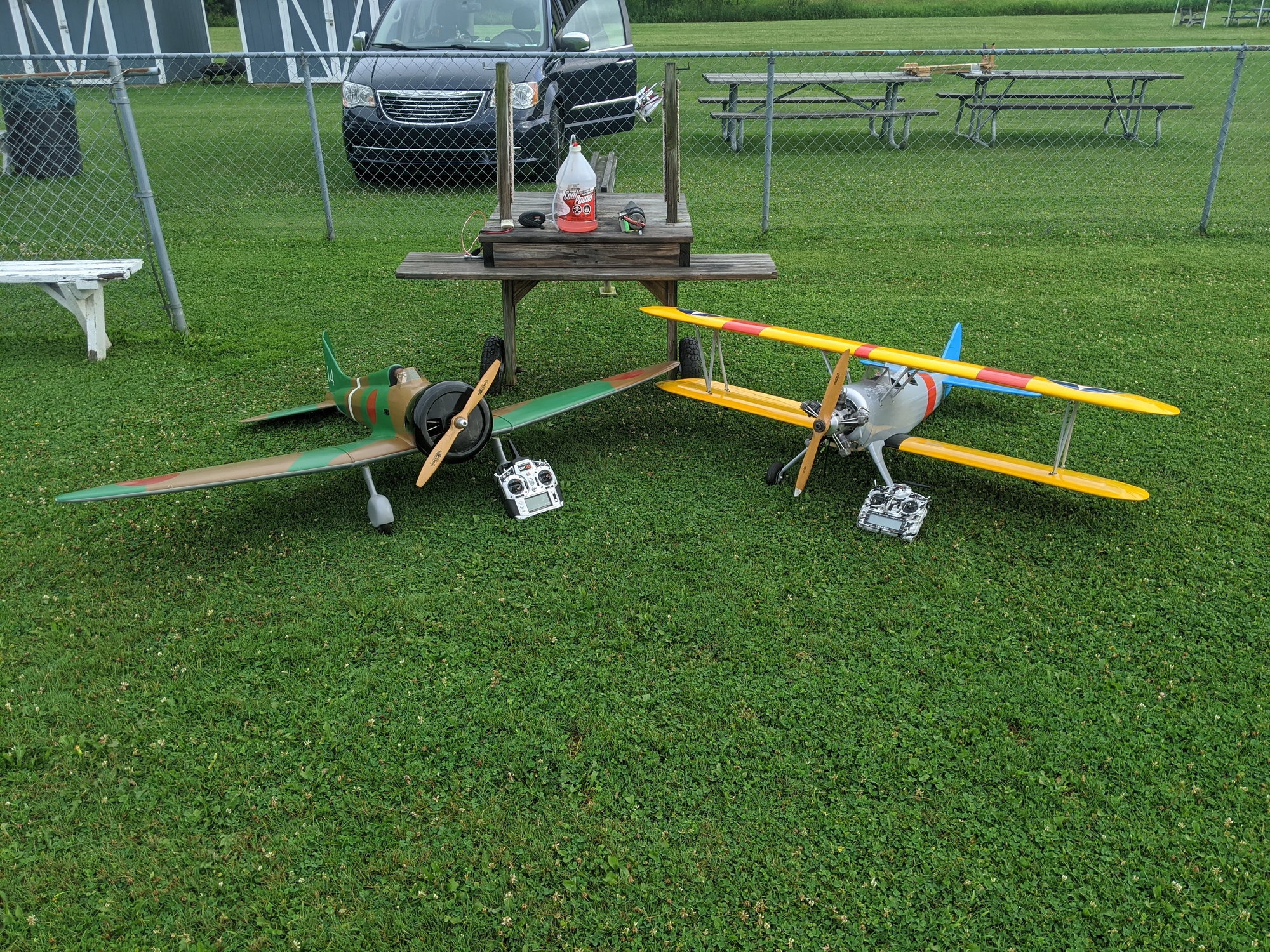
.
#89

Hello fellow enthusiasts The 125 has been converted to 40:1 Amsoil and 90 octane after break in with 32:1. I am a "if it ain't broke done fix it " The engine performed flawlessly at the field with no needle adjustments. Starts easy transitions excellent at factory settings. Developed 5854 rpm with a falcon 23/10 and flew 28 pounds with no more than 1/4 throttle on the Phoenix 60 Waco. Flew it un cowled for first flights. Baffle on. Temps 140-150 consistent across all cylinders. Very pleased with the engineThe sound on low passes is breathtaking..
Last edited by Hyjinx; 08-19-2022 at 03:59 AM. Reason: Double post
#90

My Feedback: (9)

Fitting UMS-150 to TopRCModel P-47 and prefer a semi-scale 4-blade prop. The manual spec prop is SEP 30X10 (2-blade) which turns 4800 RPM generating 28Kg thrust.
Many have fitted the Biela 23x14x4 to this model with reports of 5400 RPM on ground and under performing flight performance - not enough prop. One has shared moving to 25x14x4 (Biela?) resulted in much better performance.
Has anyone tried the SEP 4-blade prop on this engine?
https://www.sep-ls.com/25/11-26-Zoll...Hamilton-Style
https://www.sep-ls.com/26/11-26-Zoll...Hamilton-Style
My experience A:B testing the SEP vs Biela on my larger UMS-250, Moki S250 & Moki S215 shows the SEP much more efficient design.
I'm guessing this engine would turn SEP 26x16x4 or 25x18x4 to 4,000 RPM on ground and mid-4K unloaded.
Many have fitted the Biela 23x14x4 to this model with reports of 5400 RPM on ground and under performing flight performance - not enough prop. One has shared moving to 25x14x4 (Biela?) resulted in much better performance.
Has anyone tried the SEP 4-blade prop on this engine?
https://www.sep-ls.com/25/11-26-Zoll...Hamilton-Style
https://www.sep-ls.com/26/11-26-Zoll...Hamilton-Style
My experience A:B testing the SEP vs Biela on my larger UMS-250, Moki S250 & Moki S215 shows the SEP much more efficient design.
I'm guessing this engine would turn SEP 26x16x4 or 25x18x4 to 4,000 RPM on ground and mid-4K unloaded.
Last edited by marksp; 08-21-2022 at 06:18 AM.
#91

My Feedback: (62)

Mark, In my calculations, I would try a (if it exists) a 26x14x4 SEP. The engine on the ground should turn this prop at 4300 rpm. The engines true horsepower is between 7 and 7.5 horsepower. Think of a DA85 with a belt drive reduction turning a big prop. This is a lot of power. The 5-150 is a big engine and I would not operate it above 4500 on the ground. -Tom
The following users liked this post:
marksp (08-21-2022)
#92

My Feedback: (9)

Mark, In my calculations, I would try a (if it exists) a 26x14x4 SEP. The engine on the ground should turn this prop at 4300 rpm. The engines true horsepower is between 7 and 7.5 horsepower. Think of a DA85 with a belt drive reduction turning a big prop. This is a lot of power. The 5-150 is a big engine and I would not operate it above 4500 on the ground. -Tom
It's available - SEP 26X14X4 Hamilton
I’ll send note to Peter Edhofer (SEP) inquiring about the 26x14x4 Hamilton style.
Cheers
Last edited by marksp; 08-21-2022 at 09:58 AM.
#93


Fitting UMS-150 to TopRCModel P-47 and prefer a semi-scale 4-blade prop. The manual spec prop is SEP 30X10 (2-blade) which turns 4800 RPM generating 28Kg thrust.
Many have fitted the Biela 23x14x4 to this model with reports of 5400 RPM on ground and under performing flight performance - not enough prop. One has shared moving to 25x14x4 (Biela?) resulted in much better performance.
Has anyone tried the SEP 4-blade prop on this engine?
https://www.sep-ls.com/25/11-26-Zoll...Hamilton-Style
https://www.sep-ls.com/26/11-26-Zoll...Hamilton-Style
My experience A:B testing the SEP vs Biela on my larger UMS-250, Moki S250 & Moki S215 shows the SEP much more efficient design.
I'm guessing this engine would turn SEP 26x16x4 or 25x18x4 to 4,000 RPM on ground and mid-4K unloaded.
Many have fitted the Biela 23x14x4 to this model with reports of 5400 RPM on ground and under performing flight performance - not enough prop. One has shared moving to 25x14x4 (Biela?) resulted in much better performance.
Has anyone tried the SEP 4-blade prop on this engine?
https://www.sep-ls.com/25/11-26-Zoll...Hamilton-Style
https://www.sep-ls.com/26/11-26-Zoll...Hamilton-Style
My experience A:B testing the SEP vs Biela on my larger UMS-250, Moki S250 & Moki S215 shows the SEP much more efficient design.
I'm guessing this engine would turn SEP 26x16x4 or 25x18x4 to 4,000 RPM on ground and mid-4K unloaded.
I flew the toprc 47 and ums150 for its second flight today with beila 25x14x4, it takes off and flys around just fine, but i really notice the engine load and rpm drop when i pull up for a loop.
Im considering trying another prop, but all this testing is getting expensive!
The following users liked this post:
marksp (08-21-2022)
#94

My Feedback: (9)

Update - received note from Peter Edhofer, (SEP Luftschrauben). SEP 23x14x4 Hamilton style designed for and is the most proven prop for the Moki S150 warbird. "No specific data for the UMS 150; should be similar".
https://www.sep-ls.com/23/11-14-Zoll...Hamilton-Style
I’ll give this a go and report back. Good news is the UMS-150 ignition supports RPM telemetry for detailed real-time and post flight analysis which has been helpful on my UMS-250.
Cheers
https://www.sep-ls.com/23/11-14-Zoll...Hamilton-Style
I’ll give this a go and report back. Good news is the UMS-150 ignition supports RPM telemetry for detailed real-time and post flight analysis which has been helpful on my UMS-250.
Cheers
Last edited by marksp; 08-24-2022 at 05:30 AM.
#95

My Feedback: (3)

I finished my Phoenix Waco 60cc with the UMS 7-90 in it last night. Probably maiden it in the next week or two. After the engine warms up for a few minutes I'm able to get the engine to spin 5500-5700 with a Xoar 24x10 prop, which is faster than the manual says the engine can go, so I richened the needle up so it only spins 5400.
I saw some posts in a different forum about guys wanting to run 100octane or higher fuel as the engine runs cooler. Problem is where I live I can only get 100 octane that has 10% ethanol in it. I can get 110 octane without ethanol but its leaded. I'm worried about running either of these because the manual says don't run any fuel with ethanol in it, and I have no idea what a leaded fuel would do to it either. Wish I could get my hands on some 100 octane normal gas. I'm running 93 octane normal gas in it right now because its all I can get.
Anyone have any real data if the higher octane fuels actually make the engine run any cooler?
I saw some posts in a different forum about guys wanting to run 100octane or higher fuel as the engine runs cooler. Problem is where I live I can only get 100 octane that has 10% ethanol in it. I can get 110 octane without ethanol but its leaded. I'm worried about running either of these because the manual says don't run any fuel with ethanol in it, and I have no idea what a leaded fuel would do to it either. Wish I could get my hands on some 100 octane normal gas. I'm running 93 octane normal gas in it right now because its all I can get.
Anyone have any real data if the higher octane fuels actually make the engine run any cooler?
#98

Hi guys,
just found this really useful thread. I’m new to radials (and gas rather than glow engines). I’m about to complete a Flair Stearman (89 inch wingspan) and would really love to put a scale 7 cylinder radial on the front. The airframe is much lighter in build than the Ziroli and as a single cylinder the manufacturer recommends a Laser 200 or Saito 180. I’d like to maintain a scale outline and hence thinking of the UMS 7 -90 cc at 230mm diameter. Scale size but 90cc!!!!! Am I being daft putting that engine on the airframe??? Guess it’s a lot heavier than the single cylinder Saito 180 too. Could drop to the UMS 7-50 cc but significantly smaller engine diameter 195 mm v 230 mm on the 90cc variant!
im not sure whether other builders have had to add nose ballast anyway with short nose… so maybe the weight wouldn’t be too bad???
thoughts from you guys who run the UMS radials would be much appreciated.
just found this really useful thread. I’m new to radials (and gas rather than glow engines). I’m about to complete a Flair Stearman (89 inch wingspan) and would really love to put a scale 7 cylinder radial on the front. The airframe is much lighter in build than the Ziroli and as a single cylinder the manufacturer recommends a Laser 200 or Saito 180. I’d like to maintain a scale outline and hence thinking of the UMS 7 -90 cc at 230mm diameter. Scale size but 90cc!!!!! Am I being daft putting that engine on the airframe??? Guess it’s a lot heavier than the single cylinder Saito 180 too. Could drop to the UMS 7-50 cc but significantly smaller engine diameter 195 mm v 230 mm on the 90cc variant!
im not sure whether other builders have had to add nose ballast anyway with short nose… so maybe the weight wouldn’t be too bad???
thoughts from you guys who run the UMS radials would be much appreciated.
#99

Welcome MateI have a 125 five cyl on a Waco 60 ARF of similar dimensions. Fit in the cowl was a major decisive for me. The Waco ended up at 28 lbs auw and flys well with no weight on the tail. Your short nosed Flair will probably be happy without adding to the tail, but will probably fly well and be a good fit. Won't be lacking power for sure.... Low wing loaded bird anyway, weight in the tail if necessary won't be a deal breaker. Imho.
Aaron-
Aaron-
#100

Join Date: Nov 2004
Location: Nanaimo,
BC, CANADA
Posts: 83
Likes: 0
Received 0 Likes
on
0 Posts

Hi there; If you recall a while back I asked about Minnie Motors. I would like to say, I finally received the UMS 50-7 cyl. I am getting ready to run it and they say use two stroke oil. I have new oil, it is Stihl chainsaw two stroke oil, mix . UMS recommends 32-1 to break. Question, what do you fellas think of using Stihl oil will it be good on the UMS?. I also have a couple jugs of Evolution Oil, being Evolution that should be good as well. Your thoughts and what oil do you fellas use on UMS Radials.. Thank you.